Compared with airplanes and ships, although cars are made of incomparable materials, there are also many precision instruments that need to be packed in anti-rust bags. This time we will introduce in detail how the automotive industry uses anti-rust bags.
Most of the auto parts are metal components, which are easily corroded and rusted due to contact with moisture, oxygen, and acid gases in the atmosphere during production, storage, and transportation.
The technology used in the VCI bag is VCI technology, and its main function is the anti-rust agent with anti-corrosive properties.
In a sealed space, this inhibitor will change with the surrounding environment and volatilize anti-rust ions.
When they fill the entire enclosed space, they will chemically react with various substances in the air after being saturated, reducing the amount of metal Contact and reaction to protect the metal.
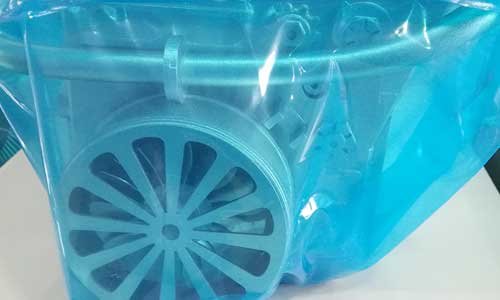
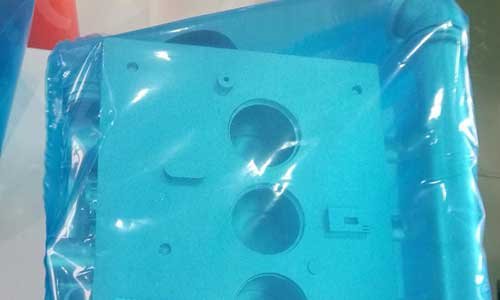
In the long-term production practice, after continuous attempts and gradual improvements in technology, people finally invented a vapor phase anti-corrosion material, which is based on the theory of vapor phase corrosion, such as the slow and continuous volatilization contained in the vapor phase anti-corrosion bag.
Molecules and groups reach a certain concentration in the packaging space and physically or chemically adsorb with the metal, thereby changing the electrode potential on the metal surface.
Effectively isolate the corrosive factors in the atmospheric environment from contacting the metal surface, so that the metal products are protected from rust.
Generally, the vapor phase anti-corrosion bags used in our auto parts are divided into two types: steel film and multi-metal film according to the material of the parts.