The packaging materials used for rust prevention are often made of a carrier with a corrosion inhibitor with rust prevention effect, and sometimes the corrosion inhibitor is used directly.
The existing anti-rust packaging materials on the market include anti-rust paper, anti-rust bag, anti-rust film and other products. So how to choose and save VCI anti-rust materials correctly?
1. How to correctly choose VCI anti-rust products and packaging solutions
1. Identify the metal type (black metal, polymetallic) of the protected workpiece, and select the anti-rust material corresponding to the metal type
2. Confirm the anti-rust period and packaging volume required by the workpiece, and determine whether it needs to be used with other auxiliary VCI products
3. Determine whether the workpiece needs to be packaged individually or arranged in layers, and choose the appropriate size and form of anti-rust material
4. Determine whether the workpiece is clean and dry and if there is oil or chemical residue on the surface of the metal part. These residual substances may react with the VCI formulation. The incompatible chemical reaction produced may cause metal rust or reduce VCI’s anti-rust effect.
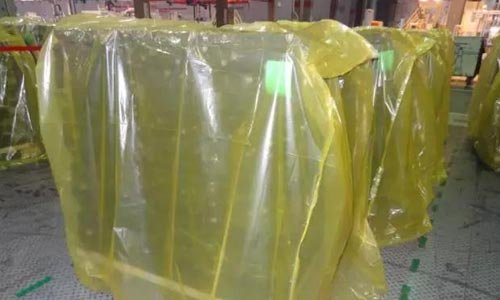

2.the correct preservation method of VCI anti-rust materials
1. Anti-rust products need to be sealed and packaged, and should not be in contact with air, which will affect the anti-rust effect;
2. It should be placed in a cool and dry place, not in the sun, which will damage the structure of anti-rust products;
3. Try to put it indoors with a lower temperature;
4. Avoid contact with fire sources and affect the quality of anti-rust paper;
5. Do not contact with acid and alkali substances;
6. The effective use date of the anti-rust paper is within one year, please use it within the warranty period for better results.
3. Correct use of VCI anti-rust products and precautions
1. Preliminary matters—Packaging operators must wear clean gloves to work to avoid direct contact with the product by hand sweat and make the product rust.
2. Early stage of packaging—Confirm that the packaged product is dry and clean, free of water stains, rust, and no other corrosive chemicals attached. If there is a foreign matter, it needs to be cleaned first.
3. Early stage of packaging — The temperature of the workpiece should be kept consistent with the temperature of the space.
4. Operating environment — The packaging operating environment should avoid excessive moisture and no acid, alkali, and other highly corrosive substances and corrosive gases.
5. Packaging process—When using anti-rust products, the side with corrosion inhibitor should face the metal product.
6. Packaging process — vci product and the workpiece must be as close as possible, the distance should not exceed 30cm, no other barrier objects can be placed between the two, the closer the distance, the better the effect.
7. Packaging process—If there are barrier materials such as paper backing boards, wood, plastic partitions, etc. between the metal to be packaged and the anti-rust film, pay special attention to the barrier materials not directly contacting the metal products. In order to avoid the barrier material contains S, CL chemical composition, affect the anti-rust effect
8. Packing space—When lining the packaging of large equipment and packing densely arranged products, it is recommended to use it with other VCI materials, such as anti-rust paper, anti-rust powder, etc.
9. Packaging is completed — After packaging, heat sealing, tape, cable ties, etc. should be used as soon as possible to seal the storage, and check that the packaged product has not punctured the film to affect the sealing effect.